数控机床液压站调试全流程指南
发布时间:2025-03-24 分类:液压站资讯 浏览量:12500
在数控机床的整机性能中,液压系统的调试质量直接影响加工精度与设备可靠性。本文基于液压传动标准,结合伺服液压站调试经验,详解从基础调试到高阶优化的全流程方法。
一、调试前准备阶段
- 硬件核查清单
- 确认液压站配置:
▪ 主泵类型(变量/定量)及额定参数
▪ 阀组功能匹配性(方向/压力/流量阀)
▪ 蓄能器预充压力(应为系统压力的25-30%) - 检测工具准备:
▪ 0.5级压力表(量程覆盖系统压力150%)
▪ 红外热像仪(温度分辨率≤0.1℃)
▪ 流量计(精度±1%FS)
- 系统预检规范
- 油液清洁度验证:
▪ 新油达到ISO标准
▪ 管路冲洗后需达到16/14/11级 - 密封性测试:
▪ 空载保压30分钟压降≤0.5MPa
▪ 24小时静态泄漏量<0.1%系统容积
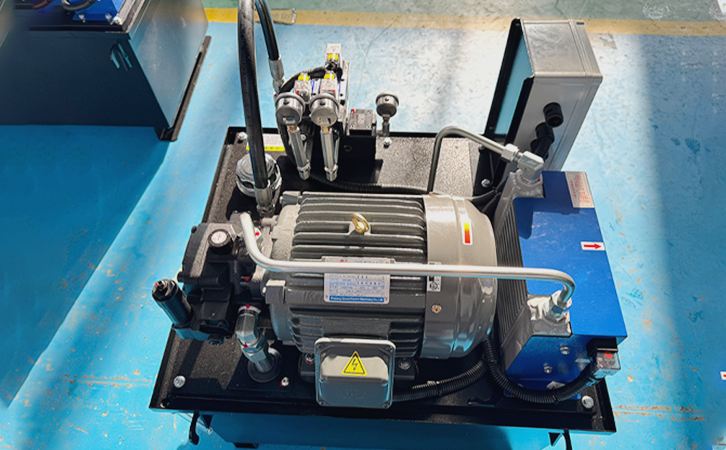
二、基础调试六步法
步骤1:动力单元空载启动
- 点动电机确认旋向正确(油液飞溅方向)
- 空载运行30分钟,检测:
▪ 泵体振动值≤4.5mm/s(GB/T 29531标准)
▪ 油箱温度温升≤2℃/10分钟
步骤2:溢流阀初调
- 逐步上调系统压力至额定值80%
- 采用PID控制时需关闭自动调节功能
- 调试工具:
▪ 溢流阀专用锁紧扳手(防止误操作)
▪ 压力阶跃测试仪(记录响应时间)
步骤3:执行机构行程校准
- 液压缸全行程往复3次排除空气
- 设置软限位缓冲(10%行程缓冲段)
- 定位精度检测:
▪ 伺服缸重复定位误差≤±0.02mm
▪ 普通缸需配合机械挡块补偿
步骤4:流量动态匹配
- 通过比例阀调整各支路流量:
▪ 快进工况:流量允差±5%
▪ 工进工况:流量允差±2% - 使用节流阀时需同步检测:
▪ 稳定流量(≤额定流量5%)
步骤5:热平衡调试
- 连续运行4小时后检测:
▪ 油温稳定在40-55℃(机床≤50℃)
▪ 冷却器进出水温差>8℃时为异常 - 热补偿设置:
▪ 黏度补偿系数设定(参考ISO VG32特性曲线)
步骤6:安全联锁验证
- 压力继电器动作值测试:
▪ 低压报警点=设定值×85%
▪ 超压停机点=设定值×115% - 紧急停止响应时间≤0.5秒
三、高阶参数优化
1. 压力脉动
- 安装位置优化:
▪ 蓄能器距泵出口≤1.5m
▪ 软管长度>300mm时需增加管夹 - 脉动控制标准:
▪ 变量泵系统≤±0.5MPa
▪ 定量泵系统≤±1.2MPa
2. 动态响应提升
- 伺服系统PID参数整定原则:
▪ 比例带:按阶跃响应超调量调整(建议5-15%)
▪ 积分时间:取系统固有频率的3-5倍
▪ 微分时间:取积分时间的1/4-1/3 - 测试信号:
▪ 频率0.1-10Hz正弦波扫频测试
3. 能效优化方案
- 采用负载敏感系统(LUDV)节能率可达40%
- 夜间模式设置:
▪ 待机压力降至工作压力30%
▪ 泵排量自动切换至维持量
四、典型故障处理指南
故障现象 | 诊断要点 | 解决方案 |
---|---|---|
压力震荡 | 检查蓄能器预充压力 | 补充氮气至设定值的90% |
执行机构爬行 | 检测油液含气量>3% | 增设真空脱水装置 |
异常温升 | 冷却器污垢系数>0.001 m²·℃/W | 化学清洗或更换翅片 |
电磁阀卡滞 | 检测线圈阻抗偏差>15% | 使用专用退磁工具处理 |
五、调试案例解析
案例1:五轴加工中心换刀故障
- 现象:刀库液压马达换向冲击导致定位偏移
- 调试过程:
▪ 在比例阀控制信号中增加5ms斜坡时间
▪ 调整缓冲阀开启压力至工作压力120% - 结果:换刀冲击力降低60%,定位精度恢复至±0.01mm
案例2:大型龙门铣横梁沉降
- 现象:横梁液压锁在停机后缓慢下滑
- 改进措施:
▪ 叠加液控单向阀(先导比1:4)
▪ 设置双路压力监测互锁 - 效果:72小时沉降量从3mm降至0.05mm
结语
液压站的精细调试需要遵循"先静后动、先粗后精"的原则。建议建立调试参数档案(包含各阀件的设定值及检测数据),并定期进行预防性维护。随着电液融合技术的发展,未来调试将更多依赖数字孪生技术实现虚拟调试,当前阶段仍需重视传统调试工艺的规范化执行。
声明:每家机床设计标准不一样,文章仅供参考!