Efficient Guide for Quickly Handling Hydraulic Station Malfunctions in Elevators
Date: 2024-11-14 Categories: News、Industry News Views: 5212
article directories[Hidden]
In modern industrial production,Lift hydraulic stationAs an important transmission and execution part, it often undertakes busy and complex tasks. However, in the process of heavy operation, malfunctions are inevitable. Timely and accurate identification and handling of these faults can effectively reduce downtime and improve production efficiency. Therefore,本文将详细解析如何快速处理提升机液压站故障,为您在日常维护中提供更为系统全面的指导。
Basic composition and principle of hydraulic station
first,Understanding the composition and operating principle of the hydraulic station of the hoist is the foundation for rapid fault diagnosis.Typically, hydraulic stations consist of hydraulic pumps, oil tanks, valve groups, filters, coolers, pressure gauges, as well as various pipe fittings and connectors.其主要工作原理是通过液压泵产生压力,推动液压油在管路中流动,从而驱动执行机构实现各种运动。掌握液压系统的工作流程,有助于快速定位故障点。
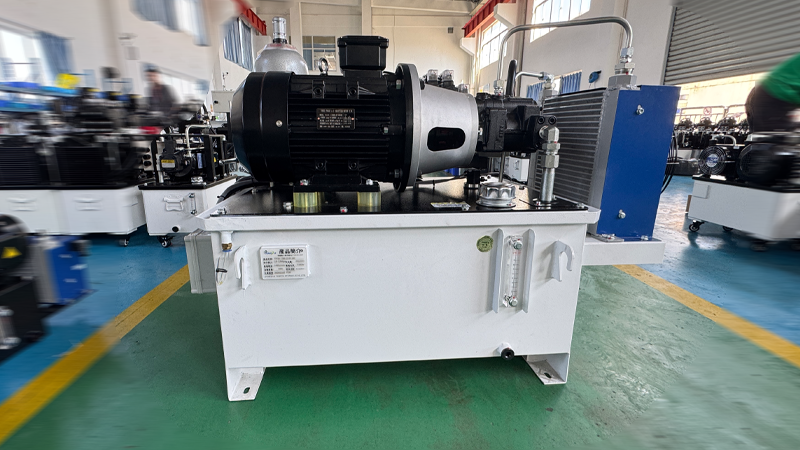
Common faults and diagnostic methods
- Hydraulic oil leakage
Leakage of hydraulic oil is one of the most common faults in hydraulic systems, mainly manifested as oil stains or insufficient system pressure.The main reasons may includeAging seals, loose fittings, or worn components.Regular inspection and replacement of seals, fastening fittings, and timely replacement of worn components are effective measures to prevent oil leakage.
- Hydraulic pump malfunction
The hydraulic pump is the heart of the hydraulic station, and its failure may cause the entire system to malfunction. Common problems include overheating of the pump body, excessive noise, and insufficient pressure. The reasons for these problems may be wear and tear of pump components, improper use of oil, or the presence of air in the system. The solution includes regular maintenance of the pump body, replacement of suitable hydraulic oil, and removal of system air.
- Control valve malfunction
The control valve is an important component for regulating the flow of hydraulic oil, and its malfunction is manifested as a blocked oil circuit or unstable operation. The cause of the malfunction may be stuck valve core, spring fatigue, or valve body blockage. This can be addressed by cleaning the valve body, checking the condition of the valve core, and replacing the fatigue spring.
- Insufficient or unstable pressure
Insufficient or unstable pressure in hydraulic systems often affects the normal operation of equipment. This may be caused by various reasons, such as insufficient hydraulic oil, clogged filter screens, or hydraulic cylinder oil leakage. For this purpose, it is necessary to regularly check the oil tank level, clean the filter screen, and inspect the sealing of the hydraulic cylinder.
Detailed steps for quickly handling faults
Step 1: Preliminary inspection and troubleshooting
Preliminary inspection is the first step in quickly dealing with hydraulic faults. Observe the status of the hydraulic station and its various components, and search for obvious signs of abnormalities. By smelling, observing, touching, and other methods, identify the oil leakage point, the source of abnormal sound, and the location of abnormal temperature.
Step 2: Use specialized diagnostic tools
Use specialized diagnostic tools such as pressure gauges and flow meters to measure the pressure, flow rate, and temperature of the hydraulic system, and determine the approximate location of the fault based on numerical values. Based on the measured values, compare them with the standard parameters of the equipment to further narrow down the scope of investigation.
Step 3: Partial disassembly and maintenance
After confirming the possible fault location, partial disassembly and maintenance can be carried out. Pay attention to marking and recording during disassembly to ensure smooth restoration. Check the condition of the disassembled components, and if they cannot be repaired, replace them with new components in a timely manner.
Step 4: Retesting and Debugging
After repair, conduct system retesting to ensure that the fault is effectively resolved. By debugging, maintain the system in its optimal operating state. Monitor for a period of time to confirm that the problem has been completely resolved.
Preventive maintenance recommendations
Quickly handling faults is certainly important, but preventing their occurrence is even more crucial. Here are some suggestions to improve the efficiency of preventive maintenance:
- Regular maintenance plan: Develop a detailed maintenance plan based on equipment usage, regularly replace hydraulic oil, inspect seals, and clean filters to maintain the system in good condition.
- Training and assessment: Provide professional training to relevant operators to enable them to understand the basic principles of hydraulic systems and quick troubleshooting methods for common faults. At the same time, regular assessments are conducted to enhance the overall technical level.
- Archive management: Establish equipment maintenance archives, record each cleaning, part replacement, and fault handling situation, and provide reference for subsequent work.
- Lubrication management: Maintain good lubrication of the hydraulic system to avoid friction and wear caused by insufficient lubrication. Use appropriate lubricants and pay attention to the quality of the oil.
- Environmental control: Keep the working environment clean, avoid dust and water vapor from entering the hydraulic system, and regularly check the temperature and humidity of the working environment.
Conclusion
By quickly identifying and handling faults in the hydraulic station of the hoist, equipment maintenance time can be effectively shortened and production efficiency can be improved. This requires not only a profound understanding of the components and principles of the hydraulic station, but also accurate judgment and decisive measures when faults occur. At the same time, it is extremely important to improve the reliability and service life of equipment through a series of preventive maintenance. By using the steps and suggestions provided in this article, I believe it can help you handle hydraulic station faults more skillfully.