Innovative Machine Tool Technology: Application and Advantage Analysis of Spindle Centered Water Discharge
Date: 2024-11-18 Categories: News、Industry News Views: 4124
article directories[Hidden]
在现代工业制造过程中,机床的主轴设计对于加工效率和精度起着至关重要的作用。随着技术的不断进步,主轴中心出水技术已经逐渐成为提升机床性能的重要手段之一。本文将从多个角度详细探讨Main spindle center water outletThe significance, implementation methods, and profound impact it brings to modern manufacturing industry.
What is spindle center outflow?
主轴中心出水,是一种创新的冷却液供应方式。传统机床使用的是外部喷水装置,也就是冷却液通过机床外部的喷嘴进行供应。然而,这种方式存在对加工精度影响较大、效率不高等问题。而中心出水则是通过主轴的内部通道,直接将冷却液供应至加工部位。采用这种方法,不仅可以显著提升加工效率,还能有效改善加工质量。
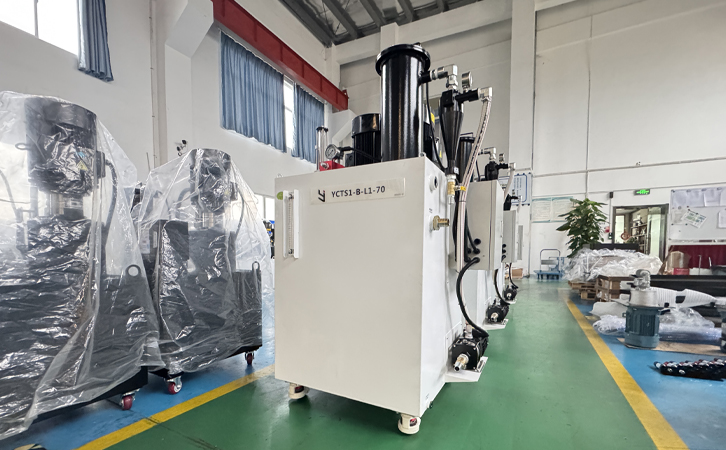
Advantages of spindle center water outlet technology
Improve machining accuracy
Through the technology of coolant delivery through the center of the spindle, the coolant can flow more directly to the point where the tool and workpiece make contact. This means that it can immediately carry away the heat generated during cutting, reducing the adverse effects of temperature on machining accuracy. At the same time, it also minimizes thermal deformation, which helps to reduce wear on machine components and maintain the stability of the entire machining process.
Enhance cooling effect
The central water outlet method can deliver the coolant more concentrated to the processing point, which is more effective than external water spray devices. This not only improves the cooling efficiency, but also better controls the temperature rise caused by the accumulation of processing heat. For some workpieces with extremely high precision requirements or materials that are difficult to process, center water discharge is undoubtedly a superior choice.
Extend tool lifespan
Cutting tools bear enormous heat and friction during the machining process. Through the central water outlet technology, this heat is quickly removed, effectively preventing rapid wear of the cutting tool and greatly extending its service life. This has significant economic value for high cost cutting tools.
How to achieve water discharge from the spindle center
To achieve water discharge from the spindle center, certain modifications need to be made to the machine tool. It mainly involves the following aspects:
Spindle structure design
To achieve the central water outlet effect, a dedicated coolant channel needs to be designed inside the spindle. This means that the existing spindle structure needs to be redesigned to ensure the integrity and tightness of the channel. The requirements for the sealing process are very high to prevent leakage.
Efficient cooling system
The supporting cooling system must be strong enough to provide a continuous and stable high-pressure coolant flow. This requires reliable cooling pumps and filtering devices to ensure the cleanliness and pressure of the coolant.
Adaptation of cutting tools
Not only do we need to improve the spindle structure, but we also need to ensure that the tools used can match the center water outlet function. This usually means designing specialized tools for this technology, such as tools with internal cooling channels, to maximize the advantages of center water outlet in the best possible state.
Industry application of spindle center water outlet
Outstanding automobile manufacturing
In the field of automobile manufacturing, due to the large number of processed parts and high precision requirements, the use of center outlet technology can effectively improve production efficiency and product quality. For example, when precision machining engine components, this technology ensures strict tolerance ranges and smoother surface quality.
Precision machining in aerospace industry
The processing requirements for aerospace components are undoubtedly extremely demanding. Through the central water outlet technology, not only can the potential of materials be fully utilized to improve the strength and wear resistance of processed parts, but also the processing cycle can be further shortened, promoting the optimization of the entire production process.
Efficient Manufacturing of Medical Devices
The precision and durability requirements of medical devices are high, and any dimensional deviation may affect their functional performance. Therefore, the central water outlet technology has also shown great potential for application in medical device manufacturing, especially in processing materials such as titanium alloys and stainless steel, where precision improvement and surface quality improvement are particularly significant.
Future Development Trends
With the continuous advancement of intelligent manufacturing, the technology of spindle center water outlet is expected to be popularized in more fields and applications. Combined with the trend of future processing automation and intelligence, further adjust the flow rate and spray angle of the coolant in real time through induction detection and big data analysis technology to achieve more intelligent and efficient processing results.
Meanwhile, future research may focus more on further reducing the energy consumption and operating costs of the central effluent system, developing more sustainable coolant solutions, and reducing the environmental impact of industrial processes.
In short, the widespread application of spindle center water discharge technology is not only the latest trend in the development of the machine tool industry, but also a revolution in the field of machining and manufacturing. By optimizing the supply of coolant, a balance can be struck between improving production efficiency, saving costs, and ensuring quality, which will have a profound positive impact on the future development of the manufacturing industry.